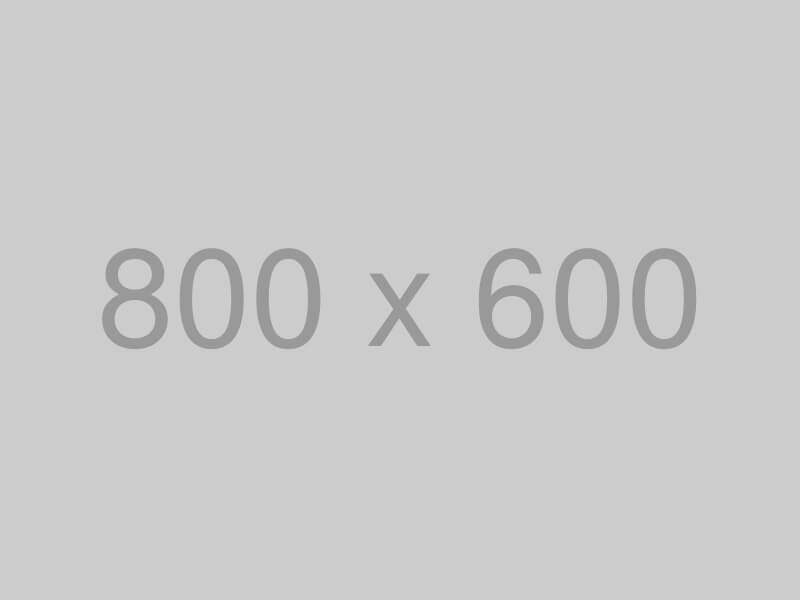
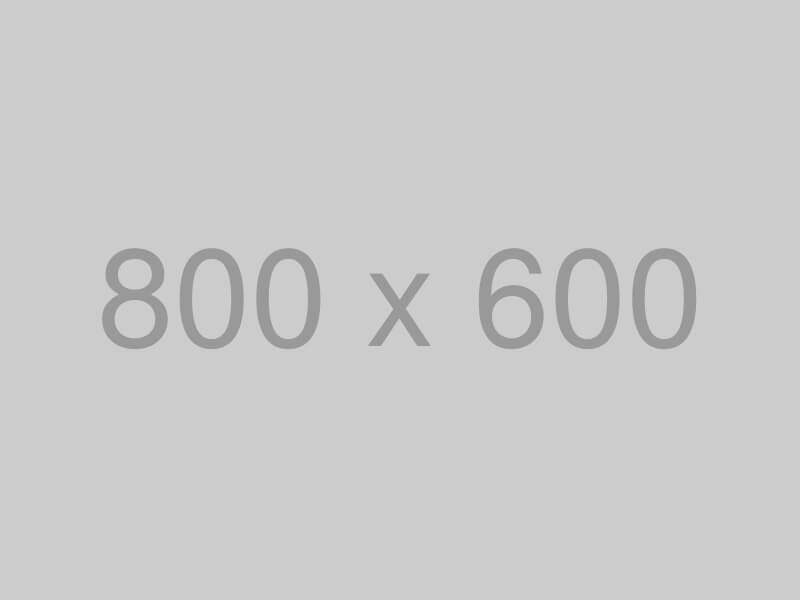
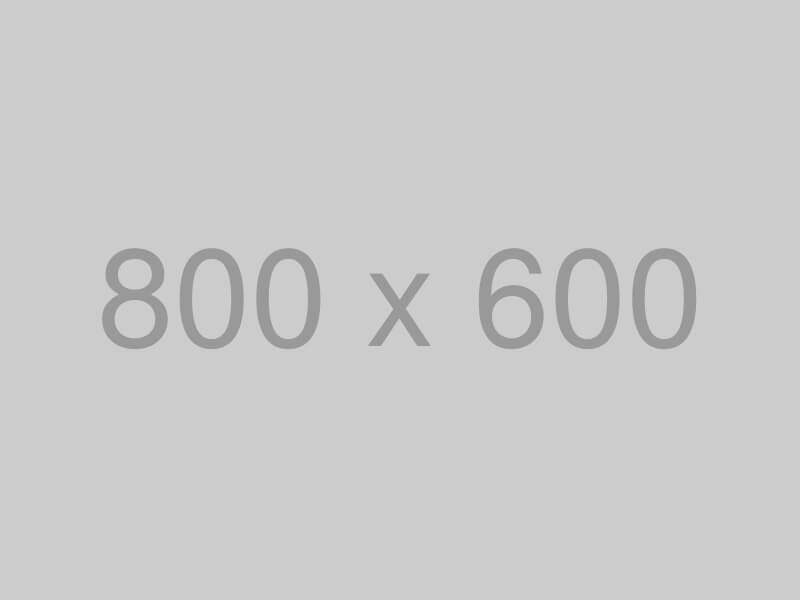
Hydraulic Crimping Couplers
✅ Ideal for Site Constraints
Engineered for projects with restricted access or limited workspace where
traditional threading or welding isn't practical.
✅ Permanent &
Vibration-Resistant Joints
The hydraulic crimping process delivers a strong mechanical lock, ensuring
stability under dynamic and static loads.
✅ No Threading or Forging Required
Eliminates the need for thread-cutting or bar-end preparation, simplifying
logistics and reducing on-site processing time.
✅ Uniform Crimping Across Sizes
Compatible with a wide range of bar diameters (Ø16 mm to Ø40 mm) while
maintaining consistent performance.
✅ Reliable Under Pressure
Tested to meet seismic and high-load demands, making them suitable for critical
structural applications.
Applications
✅ Bridges and flyovers in
high-traffic zones
✅ Tunnel linings and metro infrastructure
✅ Marine and coastal projects exposed to vibration
✅ Pile cages and deep foundation work
✅ Retrofitting and restoration in confined structures
Installation Process
- Rebars are positioned within the coupler body
- A hydraulic press is applied at predefined crimp zones
- Each zone is compressed using calibrated force
- The connection is verified for strength using crimp indicators
Advantages of Anagha Hydraulic Couplers
✅ Fast Installation – No
threading, welding, or alignment tools needed
✅ Zero Heat Impact – No
thermal stress on rebar, preserving its physical properties
✅ High-Pressure Strength – Designed to endure both
tension and compression
✅ Perfect for Prefab –
Easy integration into precast segments
✅ Enhanced Durability –
Withstands shock, vibration, and high axial loads
Quality Control Measures
✅ Each coupler undergoes
hydro-mechanical testing under simulated load conditions
✅ Crimp inspection markers ensure uniform pressure
during application
✅ All batches traceable via Unique Identification
Numbers (UIN)